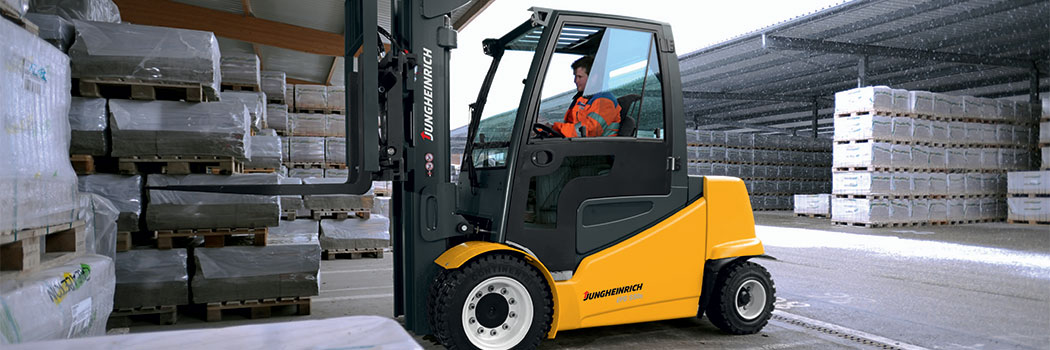
Forklifts are reaching new heights of functionality. The demand for vehicles that are efficient, safe and have the flexibility to operate effectively in a host of environments is leading to the development of models with enhanced designs and features.
Elements such as GPS tracking systems, sustainable battery-powered motors, electronic reporting and speed control are becoming prevalent, and additional upgrades are likely as operators focus on two major purchase drivers: cost containment and productivity.
Meanwhile, the proliferation of SKUs in the beverage sector is generating a greater demand for — and resulting in the launch of — forklifts that are able to retrieve pallets that are stacked higher, enable workers to easily pick specific SKUs from pallets that hold a variety of products and move seamlessly in congested areas with narrower aisles.
In addition, beverage distributors are seeking forklifts with the capacity to handle large and heavy loads, are resistant to corrosion from liquid spills, and have the traction control to keep tires from slipping in a damp environment.
For instance, Perry Ardito, general manager for Mitsubishi Caterpillar Forklift America Inc.’s Jungheinrich Warehouse Products Group, a Houston-based forklift vendor, notes that the traditional counter balance forklift, in which the forks protrude from the front of machines, is often priced at $30,000-$35,000; order pickers, in which the operator rides in a cage welded to the fork carriage and hand selects individual items from pallets, are about $35,000-$40,000; reach trucks, in which the fork carriage can reach out into the racking to retrieve pallets and is able to rise to greater heights, are in the $40,000-$45,000 range; and turret trucks, which are designed to maneuver in very narrow aisles, often range from $85,000 to $110,000.
Newer enhancements, such as the use of navigation technologies on forklifts, already are helping to cut time and expenses from the use of forklifts in distribution centers.
Other tools include radio-frequency identification (RFID) readers that are placed under trucks and work with small capsule-sized transponders that are embedded in the floors of distribution centers. The technology enables system operators to monitor the location of each forklift and issue commands to vehicles based on their locations within warehouses. Commands include the need for speed reductions, warnings about height limitations and end of aisle notifications.
The technologies also can direct forklift operators to the location of specific pallets. An arrow on the vehicle display panel indicates the direction for the driver to travel, reducing the pick cycle time.
“There is about a 25 percent increase in productivity as the system determines what path to take,” MCFA's Ardito says. “The process is quicker and uses less energy.”